Electrical hazards in electronic product manufacturing
We’re fortunate to live in a world with institutions such as UL and NEC to enforce safety regulations that keep us safe in our daily lives. Even though our wall outlets, microwave ovens, and TV sets may contain high-voltage electrical hazards within them, you seldom hear of tragic human exposure thanks to the effectiveness of these regulations.
But these safety regulations generally apply to normal use of finished products. At Lectronix where we work with bare circuit boards, and in our OEM customers’ facilities that assemble and repair products containing those boards, the risk of exposure to electrical hazards is much greater. Once the electrical circuitry is exposed, injury or death can be as simple as touching the wrong part.
In this blog we discuss electrical worker hazards and provide some basic information about electrical safety procedures and how they might be applied in an electronics manufacturing environment.
What are the types of electrical hazards?
There are two basic ways that electricity becomes a hazard to workers. Shock is experienced when the human body becomes a path for electrical current. Arc flash and arc blast arise when current flows uncontrollably through a compromised air gap between high energy conductors. The hazards of shock and arc events each require their own analysis and safety controls.
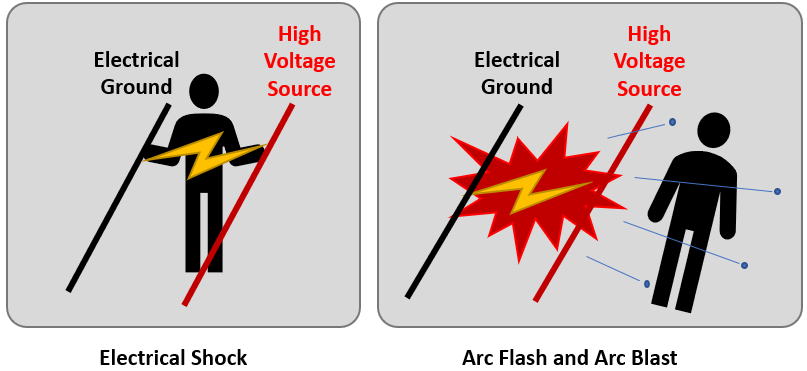
The effect of electrical shock on the human body
To have current flow through the human body, there needs to be two points of contact: one with a higher voltage source and one with a lower voltage or ground. A common example would be touching a high voltage while standing on the ground.
The effect on the human body can range from unnoticeable to fatal depending on the amount of current that flows. On the relative scale of currents that we’re familiar with in daily life, such as the 15A breaker on a typical home power outlet, it takes very little current to be dangerous.
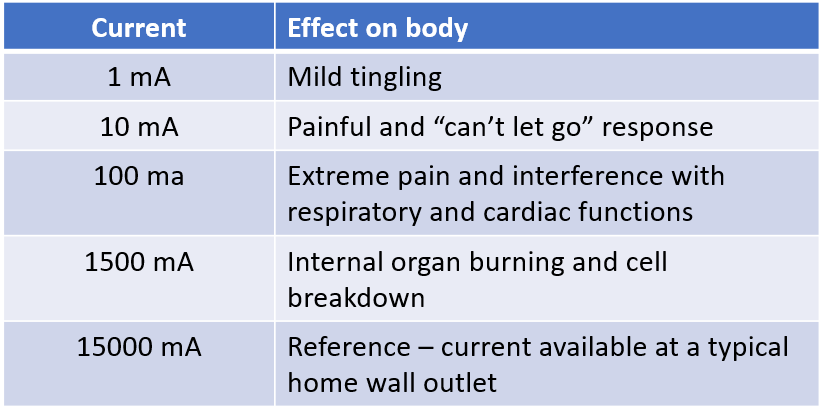
The amount of current a human body will experience depends on the voltage and the body resistance, which varies widely depending on factors ranging from sweat level to shoe selection. Due to such differences, two people touching an identical voltage may have entirely different experiences.
A good guideline in a manufacturing environment is that the presence of any voltage of 50V or more should require hazard assessment, risk analysis, and safety control plans. This level of 50V is selected because levels below that will not cause harmful currents to flow through the body under any reasonable conditions.
The dangers of arc flash and arc blast
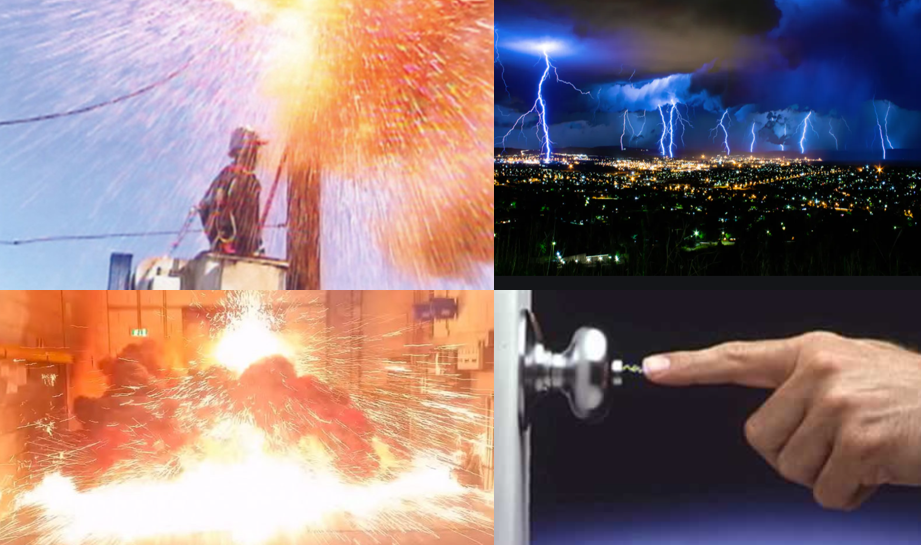
Lightning and carpet shocks are both natural occurring electrical arcs, so obviously the effects can range from benign to epic depending on the energy levels involved. At higher energies arc flash events are truly fearsome, creating temperatures more than 35,000°F, several times the surface of the sun!
At these temperatures, all materials including the conductors themselves will vaporize. When a material such as copper vaporizes it expands tremendously in volume, creating a blast filling a large radius around the event with shrapnel and molten metals.
The size and energy of an arc event depends on factors including:
- System voltage
- Fault current magnitude
- Fault duration
When working with high energy electricity, an arc event analysis is required to determine safe working distances and appropriate personal protection equipment (PPE) when working inside the danger zone. This analysis needs to be completed by someone competent. The NFPA 70E provides some tables and formulas that can guide in some cases but consider bringing in an outside consultant if there is any uncertainty in how to calculate the arc flash boundary.
Standards to help establish electrical worker safety
Federal and State Occupational Safety and Health Administrations (OSHA) is charged with ensuring safe and healthful conditions for workers. Sections §1910.331 – §1910.335 provides basic requirements for electrical safety but does not provide implementation or technical details.
The accepted standard to use in conjunction with OSHA guidelines for electrical worker safety is NFPA 70E, maintained by the National Fire Protection Agency.
NFPA 70E requires employers have a documented Electrical Safety Plan that:
- Makes “Elimination” of hazards the top priority
- #1 elimination technique is Work De-Energized
- Promotes awareness and self-discipline of employees
- For work with voltages above 50V
- Risk assessment
- Establish risk controls
- Set safe “boundaries” to keep unqualified or unprotected employees away from hazards
- Job briefings and training before work
- Lock Out / Tagout methods for ensuring safe work conditions
- Audited annually for compliance
Some basic concepts from NFPA 70E
One of the safety controls used in NFPA 70E is defined regions around an energized and exposed electrical hazard. There are separate regions set for electrical shock and arc event risks. In the illustration below, the blue regions depict the defined shock boundaries, and the red region the defined arc flash boundary. Within these regions, restrictions are applied to allow only qualified workers with appropriate PPE.
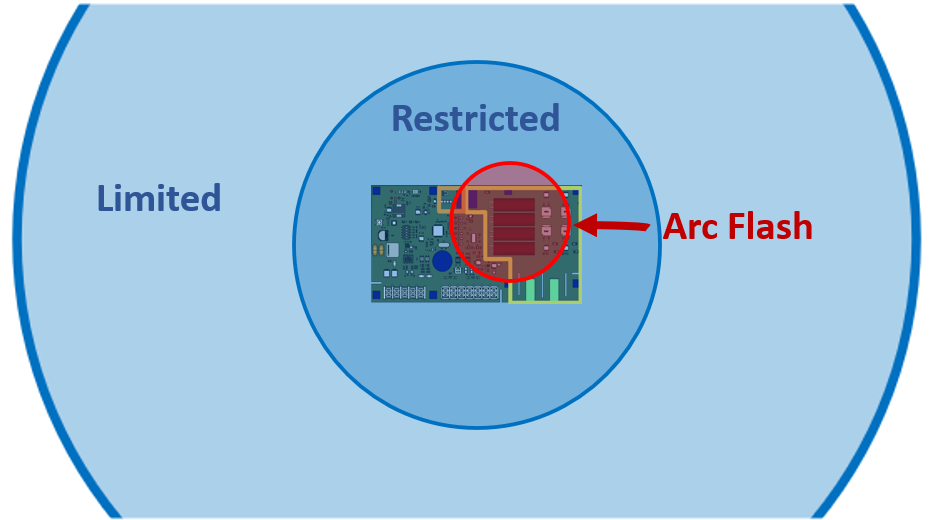
The electrical shock boundaries are set by simple table lookup based of the DC or AC voltage in tables provided by NFPA 70E. The arc flash approach boundary requires more complex calculation. Because it is based not just on the voltage but also the short circuit current and duration, the arc flash boundary can be smaller or larger than the electrical shock boundaries.
Within an electronics manufacturing facility, these regions would typically be implemented with some form of physical barrier and signage. At Lectronix we use stanchions and chains to restrict access to workstations where electrical hazards are present. Training is a mandatory aspect of NFPA 70E, and a company’s electrical safety program should describe how it is done and documented. Anyone entering the limited approach boundary around an exposed and energized circuit must meet NFPA’s definition of a “Qualified Electrical Worker” and should be trained on the task-specific safety controls and PPE.
NFPA 70E also requires the use of an Energized Work Permit process if work is going to be performed on energized and exposed hazards. This permit process brings in task-specific risk analysis and work controls and requires management sign-off to authorize the work.
Suggestions for electrical safety in electronics manufacturing
As a company that manufactures electronic products sets out to implement an electrical safety program, they may find that much of the available materials, training, and technical descriptions focus primarily on working around facility power (60Hz power) as opposed to the wide mix of circuits we encounter on boards going into diverse end products for industrial, scientific, automotive, or consumer markets.
Some Lectronix suggestions that we find helpful in our implementation include:
- The Department of Energy (DOE) provides a very useful document called “DOE Handbook Electrical Safety” (DOE-HDBK-1092-2009) that provides “cookbook” categorizations of all electrical hazards. Have a capacitor charged to 100V with 20 joules of energy in it? The handbook tables will let you look that up, determine a hazard level, and obtain recommended work practices.
- Speaking of capacitors… be sure to include them in your employee training and risk analysis. Capacitors can hold dangerous charges even after all power sources are removed from the board so they present a unique risk and require safe discharge procedures.
- NFPA 70E establishes the #1 principle as work de-energized, which is not always feasible in a manufacturing environment. At Lectronix we’ve add a second principle – work with hazardous circuitry enclosed behind a protective barrier. We have found building a custom fixture to enclose hazardous circuitry a viable alternative to exposed energized work.
- It’s common in electronic manufacturing to wear ESD heel or wrist straps. When assessing high-voltage risks, be sure to consider the voltage rating of those straps. Normally ESD gear provides a high-impedance path to ground that prevents high current flow, but if compromised by over-voltage it could turn into a short – the last thing you want when working with hazardous voltages is a grounded strap tied to the body.
- You may want to consider limiting the level of hazards your company will allow work on, to help narrow the scope of your program. For example, Lectronix forbids work with circuitry that would require Class 1 Arc Flash PPE beyond gloves. So our policy is OK with an arc flash boundary of an inch but not 3 feet.
Summary Our concerns for electrical safety extends to all: our workers, our OEM customers, the end-users, and others who our in our industry. Compliance with the NFPA 70E can seem daunting at first but is totally achievable by any company large or small. If you’d like to talk more about our program or compare notes on how to best protect workers in an electronics industry, please reach out and we’d be happy to discuss!